India’s ambition to achieve complete self-reliance in defence technology is entering a decisive phase thanks to a key improvement in the Kaveri engine—an indigenous jet propulsion system set to power next-generation air combat platforms.
Spearheaded by GTRE under DRDO, the Kaveri engine has undergone a transformative upgrade in 2025, addressing its historical limitations and aligning with the evolving demands of stealth fighters and unmanned combat drones. From enhanced thrust and thermal resilience to advanced materials and afterburner redesign, these improvements are not just technical—they are strategic.
According to India’s Defence Secretary, the engine is currently in its final testing phase in Russia, with only 25 hours of evaluation remaining. Meanwhile, the rising momentum of the #FundKaveriEngine campaign has turned public attention to the urgent need for indigenous propulsion development.
So, what exactly are the latest improvements in the Kaveri engine?
How is India tackling the thrust deficit, aerodynamic challenges, and integration for platforms like the AMCA and Ghatak UCAV?
This article breaks it down—clearly and comprehensively—covering all the upgrades, collaborations, testing milestones, and strategic significance behind India’s most critical jet engine project to date.
What’s New in 2025: Testing Milestones and Strategic Collaborations
In 2025, the Kaveri engine project will reach a critical phase. After years of developmental challenges, India’s homegrown jet engine is undergoing its final round of testing in Russia, with around 25 hours of flight trials remaining. These high-altitude and endurance tests are pivotal for certifying the engine’s integration into the Ghatak UCAV (Unmanned Combat Aerial Vehicle).
Interestingly, while the Kaveri engine was initially intended for the Tejas fighter jet, the project has strategically pivoted to meet the propulsion demands of stealth UAVs. This transition reflects a global shift in air power strategy, where next-generation unmanned platforms are gaining prominence in combat operations.
To further enhance the engine’s combat viability, GTRE has partnered with BrahMos Aerospace to redesign the afterburner. This upgrade targets the long-standing thrust shortfall, boosting afterburner output beyond 30 kN to meet the performance criteria for 4.5 and 5th-generation fighter jets.
This partnership blends BrahMos’s propulsion experience with GTRE’s indigenous design capabilities, making it a cornerstone in India’s aerospace self-reliance journey.
#FundKaveriEngine: A National Campaign for Indigenous Jet Power
Parallel to these technical advancements, a grassroots movement is gaining momentum across social media. The hashtag #FundKaveriEngine has emerged as a digital rallying cry for prioritising funding and political support for India’s indigenous jet engine program.
Citizens, defence analysts, veterans, and engineers are uniting around a shared goal: to ensure India’s defence preparedness is not hampered by reliance on foreign-made propulsion systems. The campaign has not only amplified public awareness but also pushed the Kaveri engine into mainstream defence discourse.
This public support could prove vital in accelerating the program’s timelines, especially for critical platforms like AMCA (Advanced Medium Combat Aircraft) and the Ghatak UCAV, where timely engine integration is mission-critical.
1. Enhanced Thermal Capability: A Core Improvement in the Kaveri Engine
A major improvement in the Kaveri engine lies in its thermal resilience, critical for modern combat performance. GTRE has upgraded the turbine blade technology, transitioning from traditional directionally solid blades to next-generation single-crystal blades forged from high-performance CMSX-4 alloy.
These advanced blades can now withstand extreme temperatures up to 1080°C, a noticeable upgrade over the previous 1050°C limit. To further enhance durability, they are integrated with state-of-the-art thermal barrier coatings and innovative cooling hole architectures that optimise airflow and heat dissipation.

The result? A projected increase in Turbine Entry Temperature (TET) from 1450°C to 1500°C, which directly boosts thermal efficiency, engine lifespan, and sustained performance during high-speed operations, especially in stealth fighters like the AMCA.
This critical upgrade positions the Kaveri engine closer to global benchmarks in aerospace propulsion technology, reinforcing India’s vision for self-reliant, high-performance defence systems.
2. Boosted Thrust-to-Weight Ratio: A Structural Leap in the Improvement of the Kaveri Engine
A critical improvement in the Kaveri engine revolves around enhancing its thrust-to-weight ratio, a defining parameter for modern fighter jet performance. The Gas Turbine Research Establishment (GTRE) aims to raise this ratio from the current 6.5 to a targeted 8.0, significantly improving the engine’s power efficiency without increasing its overall size.
To achieve this, engineers have introduced blisks (bladed disks) across all Low-Pressure Compressor (LPC) and High-Pressure Compressor (HPC) stages. This innovation not only reduces component weight by 25–30% compared to traditional blade-disk assemblies but also enhances rotational balance, aerodynamic efficiency, and structural rigidity, essential for supersonic flight endurance.
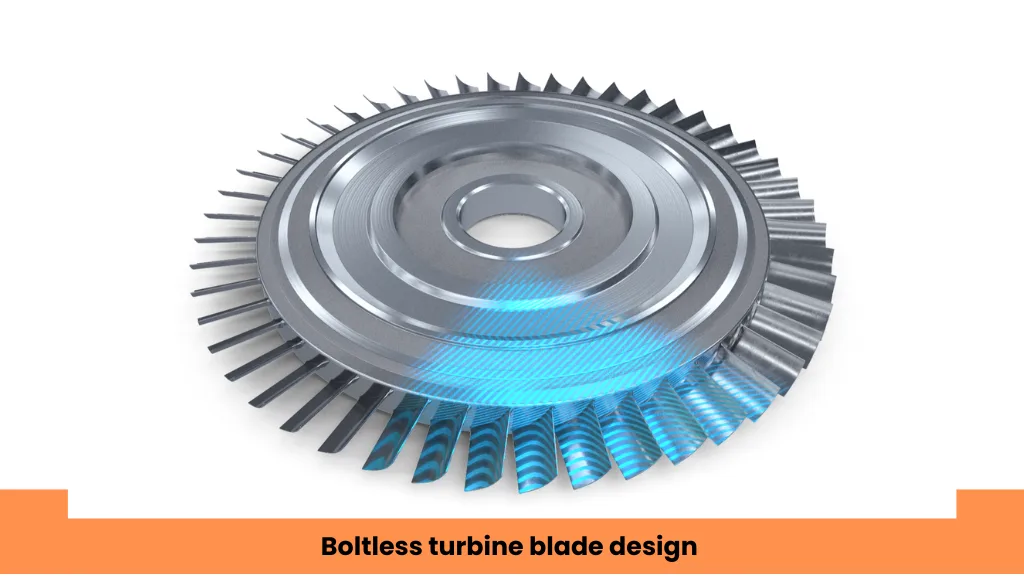
Moreover, GTRE is implementing a boltless turbine blade design, which simplifies assembly, reduces mechanical stress points, and further contributes to weight savings and high-speed durability. These structural refinements make the Kaveri engine more adaptable for next-gen fighter platforms like the AMCA and potentially for unmanned combat aerial vehicles (UCAVs) as well.
Collectively, these upgrades mark a transformative improvement of the Kaveri engine, addressing long-standing challenges in performance optimisation and paving the way for indigenous jet engine reliability at par with global standards.
3. Material Innovation: Lightweight PMC Bypass Duct – A Key Improvement in the Kaveri Engine
Among the notable advancements in the improvement of the Kaveri engine, material innovation plays a pivotal role in enhancing both performance and efficiency. One such breakthrough is the integration of a Polymer Matrix Composite (PMC) bypass duct, a significant departure from conventional metallic designs.
This advanced PMC component weighs 6 kilograms less than traditional metal ducts while maintaining the required thermal resistance and structural integrity. The weight savings contribute directly to a better thrust-to-weight ratio, which improves the aircraft’s overall agility and payload capacity.
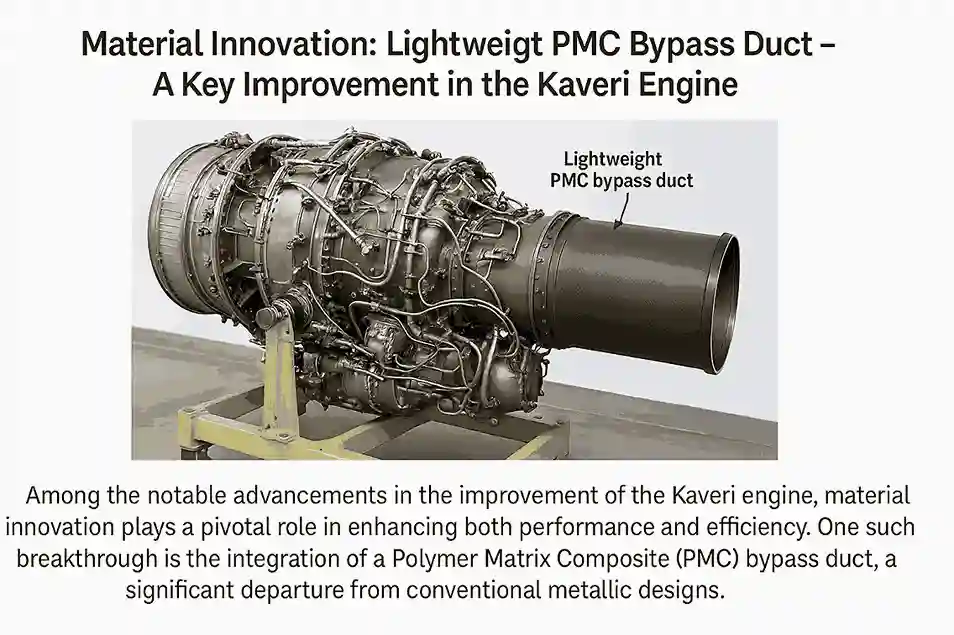
More importantly, the lightweight PMC duct reduces fuel consumption, enabling longer mission durations—an essential factor for both manned fighter jets like the AMCA and unmanned aerial systems (UAVs). The use of composite materials not only aligns with global aerospace trends but also reinforces India’s push toward next-generation indigenous jet engine technologies.
By optimising structural components with cutting-edge materials, GTRE is ensuring that the Kaveri engine upgrades meet the performance demands of future air combat platforms. This material-based innovation highlights how India is evolving from a technology importer to a self-reliant defence manufacturer.
4. Advanced Fan System: Aerodynamic Efficiency in the Improvement of the Kaveri Engine
Another major improvement in the Kaveri engine comes from its redesigned fan system, a critical upgrade for maintaining efficiency and stability in stealth aircraft configurations, such as those with serpentine air intakes like the AMCA.
To combat inlet pressure distortions—a common aerodynamic challenge in fifth-generation fighter jets—GTRE has developed a high-performance fan engineered for superior adaptability. This system offers a 25% surge margin, ensuring consistent airflow and reliability even under fluctuating intake conditions.
Key Fan Specifications:
- Efficiency: 86%
- Bypass Ratio: 3.4:1
- Mass Flow Rate: 78 kg/s
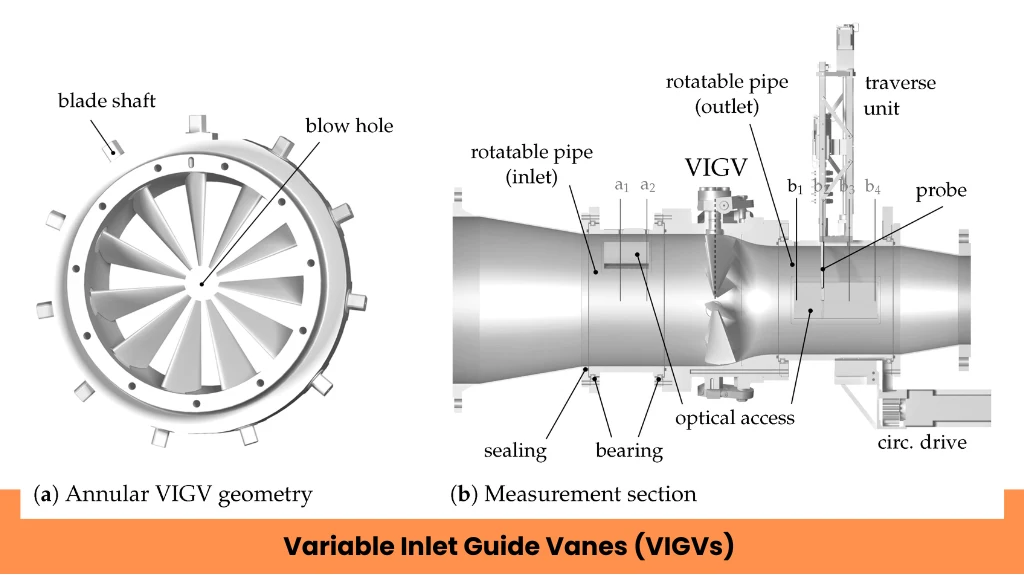
What makes this fan system truly next-gen is the integration of Variable Inlet Guide Vanes (VIGVs) paired with wide-chord blades. These design choices reduce blade flutter and improve aerodynamic control, helping stabilise airflow in both low- and high-speed conditions.
Additionally, GTRE employs 3D blade stacking techniques to minimise aerodynamic losses and enhance flow regulation. This not only improves fuel efficiency but also ensures quieter operation—a subtle yet strategic edge in modern air combat environments.
With these advancements, the Kaveri engine upgrades move closer to meeting the demands of future stealth platforms like the AMCA and Indian UCAVs, reinforcing India’s position in the race for indigenous 5th-gen propulsion systems.
5. Powder Metallurgy Discs: Strengthening the Core of Kaveri Engine
A pivotal improvement in the Kaveri engine lies in its upgraded turbine disc technology. In collaboration with the Defence Metallurgical Research Laboratory (DMRL), GTRE has introduced Powder Metallurgy (PM)-based discs, significantly enhancing the engine’s durability and thermal performance.
These PM turbine discs offer superior creep resistance, fatigue strength, and structural integrity—essential for maintaining performance in the extreme heat and pressure conditions inside a fighter jet engine.
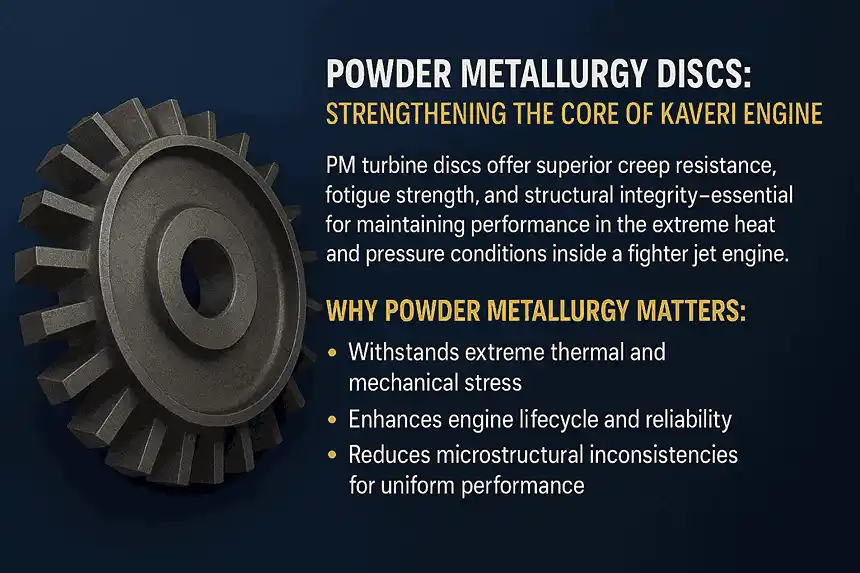
Why Powder Metallurgy Matters:
- Withstands extreme thermal and mechanical stress
- Enhances engine lifecycle and reliability
- Reduces microstructural inconsistencies for uniform performance
To support the production of these high-performance components, India is commissioning a 50,000-tonne forging press, one of the largest in the world. This ambitious step not only boosts indigenous aerospace manufacturing but also aligns with India’s goal of achieving self-reliance in critical defence technologies.
The inclusion of PM technology signals a leap forward in the GTRE Kaveri engine upgrade program, ensuring that India’s homegrown jet engine can match global standards in both durability and efficiency.
6. Afterburner Collaboration: Overcoming the Thrust Bottleneck
One of the most critical improvements in the Kaveri engine focuses on overcoming limitations in its afterburner performance—a key component for achieving thrust levels required in modern fighter jets.
While the dry variant of the Kaveri engine can generate up to 49 kN of thrust, its existing afterburner system has long been underpowered, capped at just 30 kN. This disparity has historically held back the engine’s suitability for full-fledged combat aircraft.
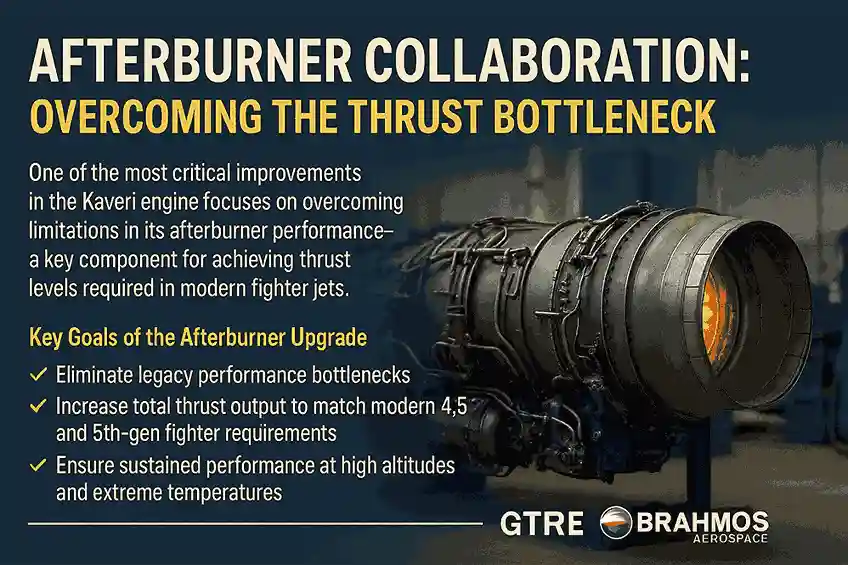
To address this, GTRE has partnered with BrahMos Aerospace in a high-stakes initiative to redesign the afterburner. This collaboration leverages BrahMos’s proven propulsion expertise and GTRE’s refined technical blueprint to create a next-generation afterburner module.
Key Goals of the Afterburner Upgrade:
- Eliminate legacy performance bottlenecks
- Increase total thrust output to match modern 4.5 and 5th-gen fighter requirements
- Ensure sustained performance at high altitudes and extreme temperatures
This GTRE-BrahMos collaboration is not just a workaround—it’s a transformative leap that could finally unlock the full potential of the Kaveri engine. By resolving its most persistent limitation, the program moves one step closer to providing India with a truly indigenous fighter jet engine capable of powering the AMCA and future UAV platforms.
Conclusion: Redefining Indigenous Power with the Kaveri Engine
The improvement in the Kaveri engine reflects India’s strategic leap toward self-reliant aerospace innovation. With upgrades in thermal resistance, thrust-to-weight ratio, advanced materials, and afterburner design, the engine is fast evolving into a next-gen propulsion system tailored for future combat aircraft.

From GTRE’s engineering breakthroughs to BrahMos collaboration, every step signals India’s intent to lead in indigenous jet engine technology. These enhancements not only close the performance gap but also lay the foundation for powering platforms like the AMCA and UCAVs.
Stay updated on India’s aerospace advancements at DefenceNewsIndia.in – your go-to source for defence, strategy, and innovation.
## Frequently Asked Questions about the Kaveri Engine (2025)
What are the key improvements in the Kaveri engine in 2025?
India’s Kaveri engine has seen major upgrades in thrust-to-weight ratio, thermal efficiency, and material innovation. Key improvements include single-crystal blades, PMC bypass ducts, a redesigned afterburner, and integration for stealth UAV platforms like Ghatak.
Is the Kaveri engine ready for use in Indian fighter jets?
According to the Defence Secretary, the Kaveri engine is in its final flight testing phase in Russia, with only 25 hours of evaluation left. It is being adapted for use in platforms such as the Ghatak UCAV and may power future AMCA variants.
What is the #FundKaveriEngine campaign about?
#FundKaveriEngine is a grassroots social media movement urging the Indian government to increase funding for the indigenous Kaveri jet engine program. It reflects growing public demand for self-reliance in critical defence technologies.